
案例简介
案件源自某自动化包装设备公司,主要营运项目为计算机、手机的自动化包装或组装产线,因包装生产线有几个特点如下:
- 当产品样式及尺寸种类多时,会使得机台共享性降低,因此功能模块的配置灵活性能降低机台的调整时间,提升包装效率。
- 包装步骤多时,传统单机做法会将每套设备都配置一套 PLC 并搭配扩充 I/O点进行分配,再将每套设备的讯号进行交握,大点数时容易出错且 PLC 使用效率不佳。
- 包装产线工站间距离长,传统点对点配线方式会耗费线材,且长距离会有电压衰减的问题。
基于上述几个产业特点,客户希望导入 iO-GRID 能够提升产线的灵活度,增加生产效率,并降低建置产线时间。
现场环境
本次案例产线各站工作项目如下流程:


产品导入
在此案例中客户使用松下 PLC 并选用放伴智能 iO-GRID C,主控与分布式 I/O 模块之间控制 16 路输入与 16 路输出模块,确保整个系统安全与可靠,丰富的诊断功能,使 PLC 主站快速监测到每个 I/O 模块的工作状态及异常状态;此外放伴智能 I/O模块每一通道采用直插式端子台,在保证工程质量的前提下大幅降低建置时间。
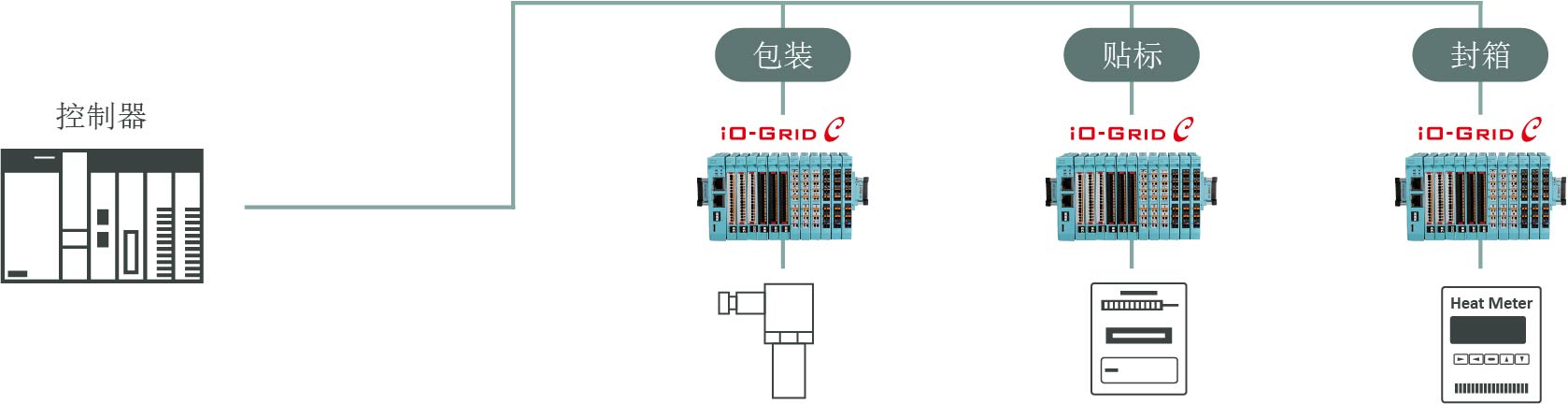

项目亮点
iO-GRID 导入包装产线后解决了客户在 I/O 配置上的点数限制困扰及庞大的成本压力,降低安装工时约 40%、系统建置成本 50%,未来客户亦可针对不同产品灵活调整产线 I/O 点数,工站距离也可弹性配置。
