iO-GRID Water Treatment System
Preserving water resources has become the world's top priority. With water shortages and the aging of industrial infrastructure for wastewater treatment, manufacturers are facing endless new challenges and increasing pressure. Among them, the demand for digitization and automation technology applications is rapidly growing. After all, intelligence is the development trend of water treatment-related industries.
Daudin provides high performance and efficient industrial automation solutions. The integration of a water treatment system controls and monitors every component with an intelligent monitoring system and a human-machine interface system. Integrating the automated solution into aging infrastructure enables you to work more efficiently and safely, thereby saving energy and costs, and allowing the original equipment to maximize its effectiveness.
System Requirement
- Various storage tanks are distributed on each floor of the factory at long distances from the master control room. If the traditional point-to-point wiring method is adopted, much wiring material would be wasted and the voltage would be significantly reduced.
- Multiple digital and analog signal points for various storage tanks with high construction cost.
- The number of storage tanks and monitoring points may be increased in the future. Therefore, the I/O extensibility and program adjustment ease is very important.
Product Used
Customer is using Mitsubishi Q Series PLC, with the requirement above the following products are integrated:
iO-GRID M series coupler module, analog I/O module, digital I/O, wire-saving relay module and USB adapter module.
Application Method
The Modbus communication method with distributed fieldbus I/O can collect the sensor data of equipment in each station to timely monitor the water level of the storage tank and related wastewater concentration and operate the control valve.
Project Highlight
Solve wiring problems for long distances between factory machines without rewiring and greatly reduce construction manpower and the wiring time and cost.
- l Only one PLC is required for distributed control to save wiring cost by over 40%.
- Comprehensive digital and analog product lines, with competitive price points to save users by over 50% integration cost compared to conventional expansion I/O.
- Flexible configuration with great extension capabilities.
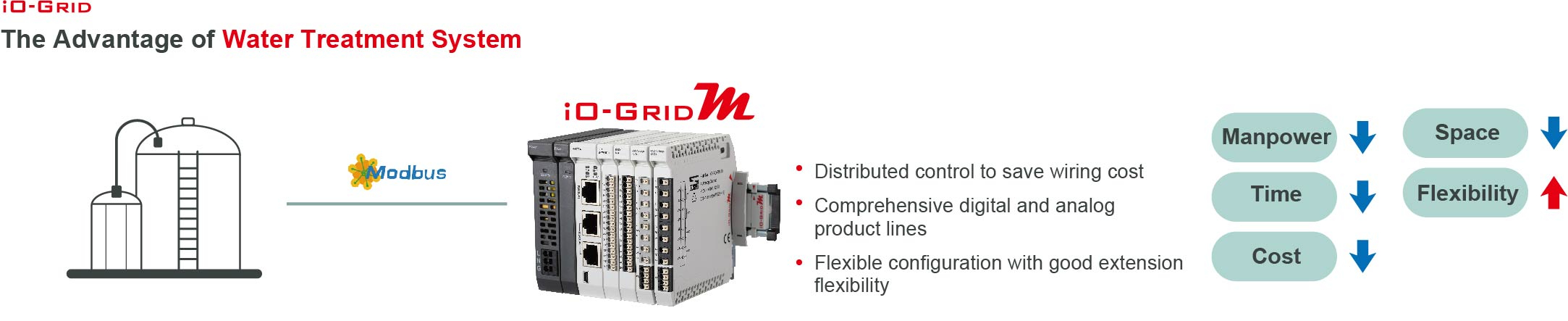