汽車零件生產線案例
案例簡介
案件源自某自動化設備公司,主要營運項目為汽車零件生產設備,因汽車零件生產線有幾個特點如下::
- 零件樣式多,生產設備從單機到流水線都有,控制器會依照製程工法不同,會有多款機型搭配使用,使得設備管理成本增加,且設備的使用效率不佳
- 單機設備中電控盤空間有限,電器元件的尺寸越小,電控盤設計及配線更為彈性
- 流水線各站製程依序連貫,當有其中一站發生異常時,會使得整條生產流程中斷,因此設備的異常檢測及排除時間要求高
基於上述幾個產業特點,客戶希望藉由 iO-GRID 體積薄、可與各間 PLC 廠牌相容並長距離控制等特點,導入在生產機中,降低設備建置成本。
現場環境
本次案例生產機台如圖,金屬零件會在單一機台進行加工,加工後經由輸送帶傳送至下一工站,當加工程序都結束後進行組裝及檢測,完成零件生產
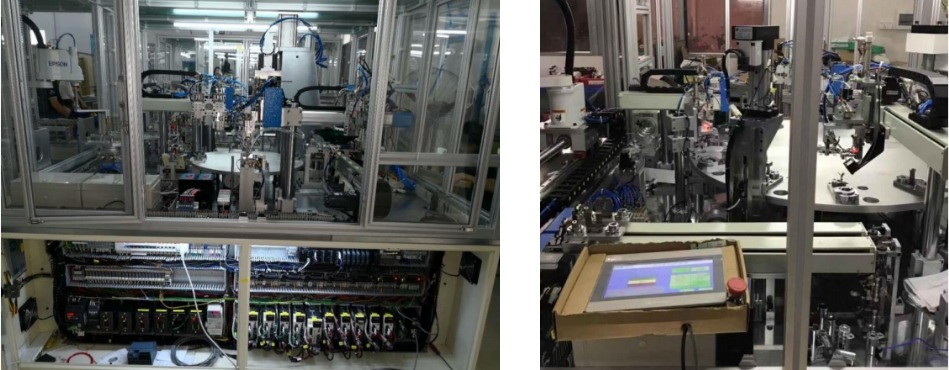
產品導入
在此案例中客戶使用基恩斯 PLC 並搭配放伴智能 iO-GRID C控制機台,配置架構如圖所示。
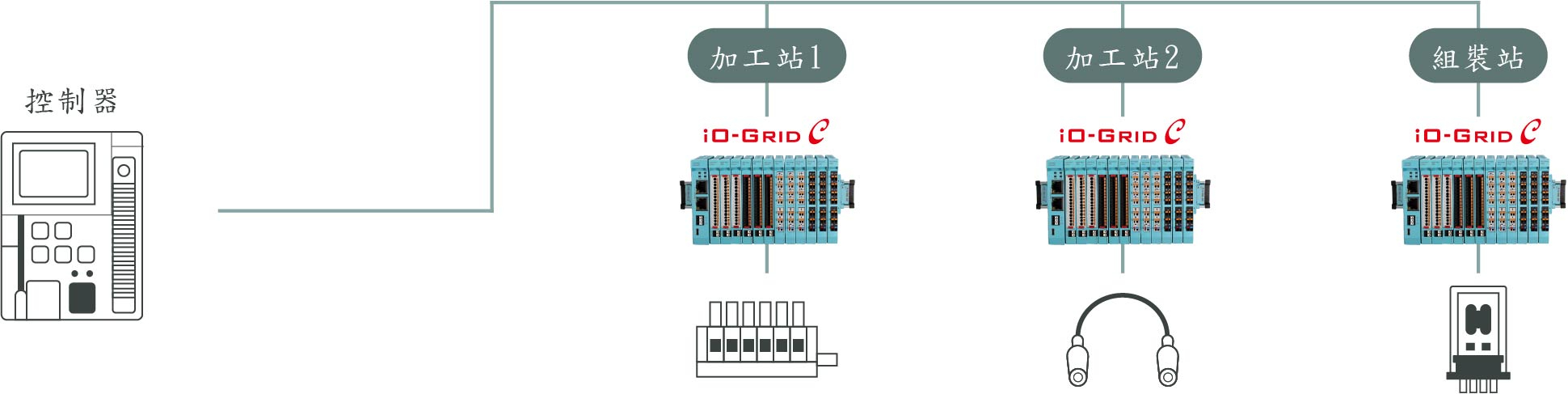
由於機台盤內空間十分有限,已無多餘空間可以安裝 I/O 模組,正是發揮 iO-GRID尺寸薄且可以長距離控制的特點,將 I/O 模組置放於機台空位處,完全不受盤內空間限制。
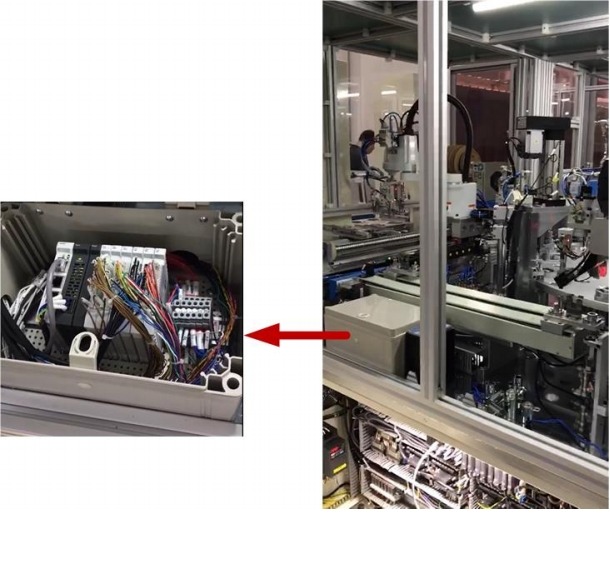
項目亮點
iO-GRID 導入生產機台後解決了客戶配電盤空間不足的問題,I/O 模組尺寸薄僅12mm 大幅節省盤內空間,且 iO-GRID 採用 Modbus 通訊協議,可搭配各間廠牌的 PLC 使用,使 I/O 模組共用性高容易管理,大幅降低硬體成本 40%,節省控制櫃體空間 50%。此外,當有異常發生時,iO-GRID 警示燈立即亮起,並回覆異常碼告知上位機,快速進行故障排除,不必擔心生產中斷的問題。
